Introduction
Diesel generators play a crucial role in providing backup power in various settings, including industrial facilities, construction sites, data centers, hospitals, and remote locations. However, in dusty environments, diesel generators face unique challenges that can impact their performance and longevity. Dust and debris can clog air filters, cooling systems, and other components, leading to reduced efficiency, increased maintenance requirements, and potential breakdowns. To ensure reliable operation in dusty conditions, it is essential to optimize diesel generators with appropriate design features, maintenance practices, and operational considerations.
Understanding the Challenges of Dusty Environments
Dusty environments present several challenges for diesel generators that can compromise their performance and reliability. Dust particles, especially fine particles, can infiltrate the generator's intake system and clog air filters, reducing the flow of clean air to the engine. This can lead to incomplete combustion, decreased power output, increased fuel consumption, and higher emissions. Moreover, dust accumulation on the generator's cooling system can impair heat dissipation, resulting in overheating and potential damage to critical components.
In addition to the direct impact on the generator's performance, dust can also accelerate wear and tear on moving parts, such as pistons, cylinders, and bearings. Abrasive dust particles can cause friction and premature wear, leading to increased maintenance requirements and shorter lifespan of the generator. Furthermore, excessive dust buildup can create electrical hazards, such as short circuits and overheating of electrical components, posing safety risks to personnel and equipment.
Design Features for Diesel Generators in Dusty Conditions
To mitigate the impact of dust on diesel generators, manufacturers incorporate various design features that enhance the generator's resilience in dusty environments. These design features are aimed at improving air filtration, cooling efficiency, dust protection, and overall durability. Some of the key design considerations for diesel generators in dusty conditions include:
1. Enhanced Air Filtration Systems: High-efficiency air filters are essential for preventing dust ingress into the generator's engine. Manufacturers utilize advanced filtration technologies, such as dual-stage filters, cyclonic separators, and pre-cleaners, to remove dust particles of different sizes before they reach the engine. Regular maintenance and replacement of air filters are critical to ensure optimal filtration performance.
2. Sealed Enclosures and Gaskets: Dust-proof enclosures and gaskets are designed to prevent dust infiltration into sensitive components of the generator, such as the engine, alternator, and control panel. Sealed enclosures with proper ventilation ensure that internal components remain clean and protected from dust contamination.
3. Improved Cooling Systems: Dust can impair the cooling efficiency of diesel generators by blocking radiator fins, heat exchangers, and cooling fans. Generators designed for dusty conditions feature robust cooling systems with larger radiators, self-cleaning fans, and protective screens to prevent dust buildup and maintain optimal operating temperatures.
4. Dust-resistant Coatings and Materials: Components exposed to dust are often coated with protective finishes or made from corrosion-resistant materials to withstand abrasive particles and environmental conditions. Powder coatings, zinc plating, and stainless steel construction are commonly used to enhance the durability of critical components.
5. Dust Seals and Shields: Dust seals and shields are installed in strategic locations to prevent dust intrusion into bearings, electrical connections, and moving parts. Sealed bearings, dust caps, and protective covers help minimize the risk of contamination and extend the lifespan of components exposed to dust.
Maintenance Practices for Diesel Generators in Dusty Environments
In addition to proper design features, regular maintenance is essential to ensure the optimal performance and longevity of diesel generators operating in dusty conditions. Dusty environments accelerate the accumulation of dirt and debris on the generator's surfaces, requiring more frequent inspections, cleanings, and replacements of components. Implementing the following maintenance practices can help mitigate the impact of dust on diesel generators:
1. Scheduled Inspections: Regular visual inspections of the generator's exterior and interior components are necessary to identify signs of dust accumulation, wear, or damage. Inspect air filters, cooling systems, electrical connections, and moving parts for dust buildup and clean or replace as needed.
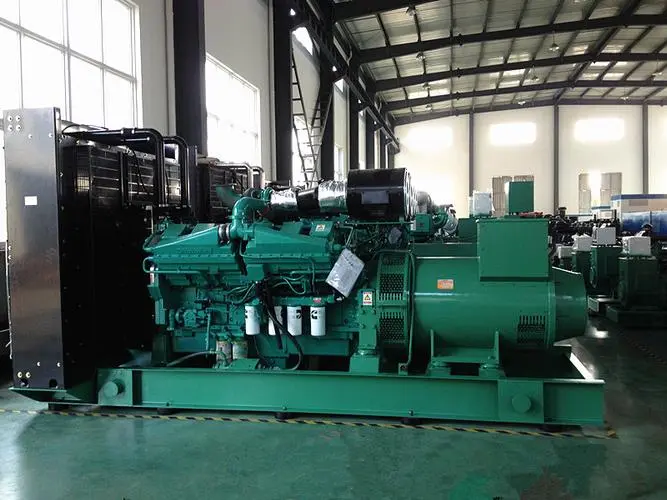
2. Air Filter Maintenance: Air filters are critical for protecting the engine from dust contamination. Check air filters regularly and clean or replace them according to the manufacturer's recommendations. Use high-quality filters with the appropriate filtration efficiency for dusty environments.
3. Cooling System Cleaning: Dust can obstruct the cooling system, leading to overheating and reduced efficiency. Clean radiator fins, heat exchangers, and cooling fans regularly to remove dust and debris. Ensure that airflow is unobstructed for optimal heat dissipation.
4. Electrical Component Inspection: Dust can compromise the electrical connections and components of the generator, increasing the risk of malfunctions and safety hazards. Inspect electrical connections, terminals, and wiring for dust buildup and clean them using compressed air or a soft brush.
5. Lubrication and Greasing: Dusty environments can accelerate the wear of moving parts and bearings due to abrasive particles. Ensure proper lubrication of bearings, pistons, cylinders, and other moving components to reduce friction and extend their lifespan. Use lubricants recommended by the manufacturer for dusty conditions.
Operational Considerations for Diesel Generators in Dusty Conditions
In addition to design features and maintenance practices, certain operational considerations can help optimize the performance and efficiency of diesel generators in dusty environments. Operators and maintenance personnel should follow best practices to minimize the impact of dust on the generator's operation and ensure reliable power supply. Some key operational considerations include:
1. Proper Placement and Ventilation: Install diesel generators in dust-prone areas away from sources of dust generation, such as construction sites, unpaved roads, and industrial processes. Ensure that 150kw diesel generator for remote mining sites is placed on a level, stable surface with adequate ventilation to prevent dust buildup and overheating.
2. Regular Load Testing: Periodic load testing of diesel generators is essential to verify their performance under varying load conditions. Dusty environments can impact the generator's efficiency and power output, so regular testing helps identify any issues and ensure that the generator can meet the required load demand.
3. Fuel Quality and Storage: Use clean, high-quality diesel fuel to prevent fuel system contamination and ensure optimal engine performance. Store fuel in a clean, dry environment with proper filtration and ventilation to avoid dust ingress into the fuel tank and fuel lines.
4. Emergency Response Plan: Develop an emergency response plan for unexpected events, such as dust storms, extreme weather conditions, or equipment failures. Ensure that personnel are trained in proper shutdown procedures, troubleshooting techniques, and safety protocols in case of generator malfunction due to dust-related issues.
Conclusion
Diesel generators are indispensable for providing backup power in dusty environments, but they face unique challenges that can affect their performance and reliability. By optimizing diesel generators with appropriate design features, maintenance practices, and operational considerations, operators can mitigate the impact of dust and ensure the uninterrupted operation of critical systems. Understanding the challenges of dusty environments, incorporating dust-resistant design features, implementing regular maintenance practices, and following operational best practices are essential for maximizing the efficiency and lifespan of diesel generators in dusty conditions. By taking proactive measures to protect diesel generators from dust contamination, operators can maintain a reliable power supply and minimize downtime in challenging environments.